When a power converter doesn’t require very high power – i.e. 200 watts or less – flyback converters are good choices due to their lower cost, decreased quantity of components, and simple design. Flyback converters are used in a variety of equipment, including televisions, LED lighting arrays, telecommunications, and industrial systems. One of the main…
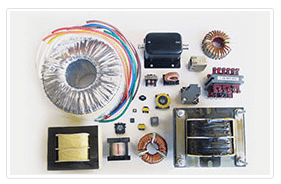
Manufacturing & Magnetics – An Important Industry Outlook
With 2017 officially closed, now is the time to look towards industry predictions in the new year. Industry Outlook Predictions Projections for 2018 show positive outlooks for three of the main industries MPS serves. The renewable energy sector, both globally and within the U.S., will always be at the forefront of debate and conversation. Renewables (in…
2017 Expansion Plans to Benefit Our Customers
2016 was a pivotal year for magnetic components. The presence of hydroelectricity, wind electricity and solar power was felt in a significant way as countries around the world pushed for clean and renewable sources of energy. In conjunction with this trend, electric cars also contributed to the green drive making waves across the planet. At…
Off-Road Segment Gets A Hybrid Upgrade
Popularity among hybrid and electric vehicles have grown exponentially within the U.S. Tesla has stated they spend $0 on marketing yet demands have continued to grow. In fact, think about how you’ve never seen any ads or commercials from Tesla. With no marketing power how can it have such strong potential to take over the…
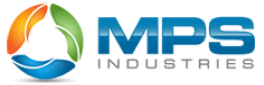
Save the Date: The AES Expo is Around the Corner!
In manufacturing, one of the most valuable, important things you can do is get out there and interact with your clients and industry leaders. And one of the best ways to do this is by attending trade shows. When you spend time at a trade show, you have the invaluable opportunity to interact with current…
The Force Between our Magnetic Components and the Auto and Energy Industries
We take great pride in the production of our magnetic components, and we continue to improve their quality and capabilities as technology continues to change the manufacturing world. It’s always interesting for us to see how our magnetic components fit into specific applications, which can range from a variety of different industries. Recently, we have…
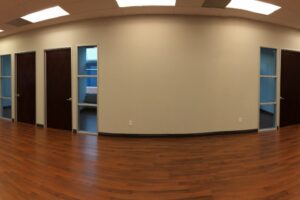
A New Year and a Brand New Facility
One of the most exciting things in a company’s history is expansion – it is a tangible and meaningful measurement of growth and success, and it confirms and encourages the hard work that all of the employees have put in in the years before, and an impetus to continue and progress. We think it’s fitting…